Background
The Centre for Renewable and Sustainable Energy Studies (CRSES) at Stellenbosch University, supported by the SOLTRAIN 2 project, approached Cape Brewing Company (CBC) with the proposal to investigate the possibility of using solar thermal (ST) technology to produce hot water for the brewery and thereby reducing their paraffin fuel consumption and boiler load. A pre-feasibility study was conducted by CRSES indicating that a ST system of about 120 m2 collector area and 10 000 litre storage would provide 60 % of the existing hot water needs and be a good investment, especially considering the EUR 11 000 subsidy from SOLTRAIN 2. With favourable pre-feasibility results CBC decided to proceed with the tender process. After an on-site walkthrough and opportunities for questions and answers, ten proposals were received, all from South African companies. From these candidates a shortlist was prepared which were then interviewed until a final decision was made on the best candidate to install the solar thermal system.
The System
In Figure 1a, the installed collector array at CBC can be seen. The collector array consists of 12 GREENoneTEC GK3102 collectors, each with a gross area of approximately 10 m2. The collectors are arranged in three rows of four collectors each, providing a gross collector area of approximately 120 m2. The system has a 10 000 litre solar buffer storage including three-way stratification as shown in Figure 1b.
The solar thermal system consists of a solar loop, charging loop and discharge loop as shown in Figure 2. The solar loop working fluid is a water-glycol mixture driven by a variable-speed pump. The system is protected against overheating by an active safety cooler, but also has standard good practice measures implemented (or available) such as hydraulic design for favourable draining behaviour, night cooling through the collectors and pressure safety valves. Water from the solar buffer storage is heated by the solar loop through a custom built heat exchanger which separates the glycol from the brew water. All components on the charging and discharge loops, including the heat exchanger, are made of stainless steel.
The solar buffer storage tank is charged using three-way external stratification (see also Figure 1b). Integration of the new system occurs at the original hot water storage. From the original hot water storage, all hot water needs are drawn and then replenished by the water from the solar buffer storage. The original hot water storage and solar buffer storage operate at atmospheric pressure which is lower than the solar loop pressure. To reduce the risk of leaks through the heat exchanger (due to higher pressure on the solar loop side of the heat exchanger) a pressure step-down valve is used to raise the pressure on the charging loop side of the heat exchanger to higher than the solar loop side. After the step-down valve, the pressure is reduced to atmospheric at which the storage tanks operate.
Performance Calculations
To calculate the system performance, simulations were conducted using the Polysun software. The CBC hot water demand profile, at the time of the tender, was estimated to be 7 000 litres/day at 85 °C (the demand has increased significantly since). For simulation purposes the demand was distributed equally over the day starting at 01h00 and ending at 19h00, according to the operation schedule. The brewery typically operates for 245 days per year, excluding on weekends, public holidays and a two week summer holiday period in December. The available roof area was approximately 190 m2, orientated north-east and has a 15° tilt.
In Figure 3, the simulated solar contribution to the final heat demand is shown for one year. The variability in the demand is influenced by the varying absences due to number of weekends and holidays during each month. The solar gains (Qsol) follow the seasonal trend with very high solar fractions (SF) in summer (almost 90 % in January) and significantly lower contributions in the winter (42 % in July), which is also the local rainy season. The data show that there is always a need for the auxiliary heat source (boiler), due to the heat demand in early morning, but also because special care was taken not to oversize the system at any period of operation.
The overall simulation results and economic performance figures are provided in Table 1. The internal rate of return (IRR) is approximately 17 % indicating that the system is a good investment. The CBC solar system is one of only a handful of process heat applications in South Africa that are pioneering this market segment; it uses state-of-the-art large 10 m2 collectors and has a custom-built stainless steel heat exchanger and tank that includes stratification.
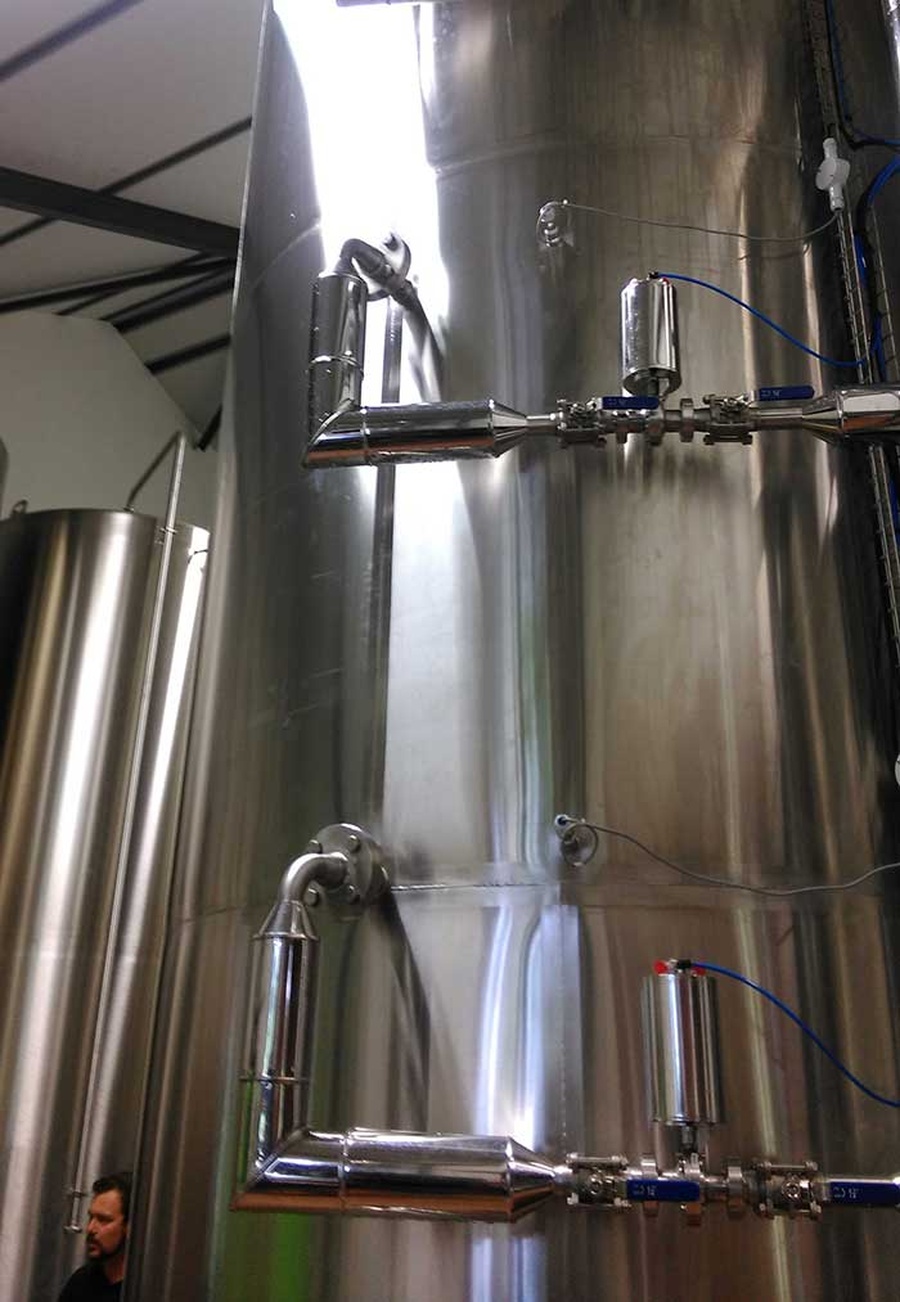